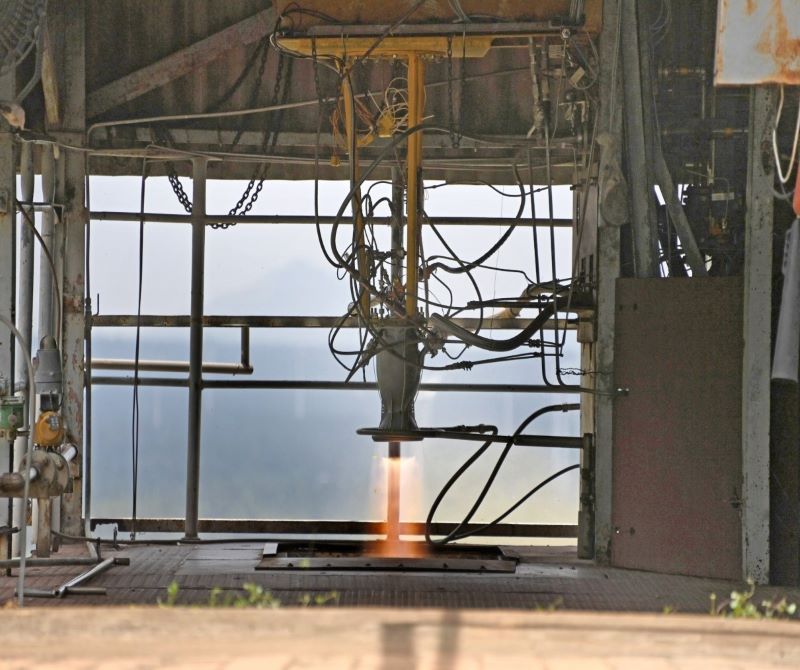
ISRO conducts successful hot testing of liquid rocket engine manufactured through Additive Manufacturing
Indian Space Research Organisation (ISRO) said it has achieved a 'major milestone' with the successful hot testing of liquid rocket engine manufactured through Additive Manufacturing (AM) technology for a duration of 665 s on May 9, 2024.
The engine used is the PS4 engine of PSLV upper stage.
"The PS4 engine manufactured in the conventional machining and welding route has been in use for the fourth stage of PSLV which has a thrust of 7.33 kN in vacuum condition. The same engine is also used in the Reaction Control System (RCS) of the first stage (PS1) of PSLV," ISRO said in a statement.
The engine uses the earth-storable bipropellant combinations of Nitrogen Tetroxide as oxidizer and Mono Methyl Hydrazine as fuel in pressure-fed mode and was developed by the Liquid Propulsion Systems Centre (LPSC), ISRO.
LPSC redesigned the engine making it amenable to the Design for Additive Manufacturing (DfAM) concept thereby gaining considerable advantages.
The Laser Powder Bed Fusion technique employed has brought down the number of parts from 14 to a single-piece, and eliminated 19 weld joints, saving significantly on the raw material usage per engine (13.7 kg of metal powder compared to the 565 kg of forgings and sheets for conventional manufacturing process) and reduced 60% in the overall production time.
The manufacturing of the engine was done in the Indian industry (M/s WIPRO 3D), and the engine was hot tested at ISRO Propulsion Complex, Mahendragiri.
Support Our Journalism
We cannot do without you.. your contribution supports unbiased journalism
IBNS is not driven by any ism- not wokeism, not racism, not skewed secularism, not hyper right-wing or left liberal ideals, nor by any hardline religious beliefs or hyper nationalism. We want to serve you good old objective news, as they are. We do not judge or preach. We let people decide for themselves. We only try to present factual and well-sourced news.